Solar Construction Automation with Matt Campbell, Terabase Energy | EP 165
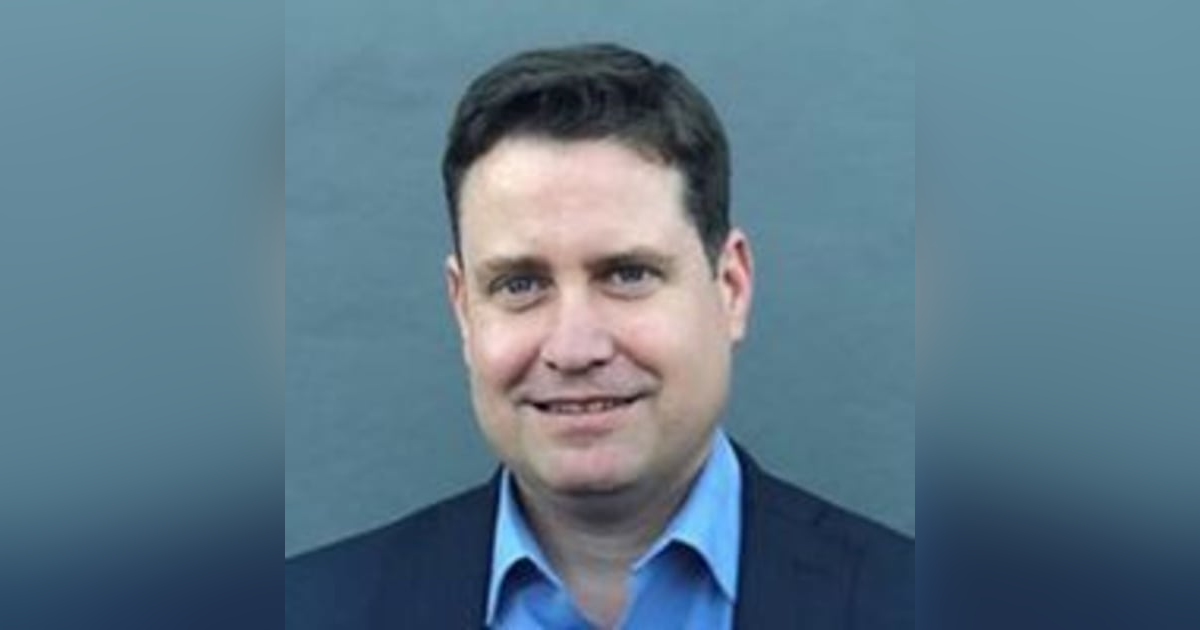
Please take our listener survey.
Terabase Energy is revolutionizing large-scale solar construction with a combination of digital platforms and robotics to reduce costs and accelerate deployment. Today on the Clean Power Hour, Terabase Energy CEO Matt Campbell joins Tim Montague to discuss their groundbreaking construction automation system, featuring a unique blend of physical robots and digital technology.
Discover how Terabase's "pop-up factory" is transforming solar construction by eliminating heavy lifting and reducing worker injuries. Robots take charge of unloading and moving panels, while skilled workers focus on finer assembly tasks. The result? A remarkable 25-50% boost in productivity, with a recent pilot installing a staggering 1300 panels in just one day, all thanks to the power of automation.
But that's not all – Terabase's digital platform takes construction management to the next level. It tracks material flow, optimizes construction sequencing, and provides real-time progress updates, bringing unprecedented visibility to construction sites.
Join us as we explore how Terabase Energy is piloting and refining this cutting-edge system in collaboration with industry giants like First Solar. Their plan for large-scale deployment in 2023 promises not only quality and reliability but also a solution to address labor shortages and reduce costs.
In an era where sustainability is paramount, Terabase Energy's innovative construction automation system could be the game-changer the solar industry needs. Don't miss out on the future of solar construction – watch now! 🌞🤖
Key Takeaways
- What is Terabase Energy's innovative construction automation system?
- How does Terabase Energy's "pop-up factory" reduce worker injuries?
- What benefits does the automation provide?
- What does the digital tracking platform offer for construction management?
- What are Terabase Energy's plans for the future, and how does their innovation impact the solar industry?
Terabase Energy
Matt Campbell
Terabase Energy LinkedIn
Connect with Tim
Clean Power Hour
Clean Power Hour on YouTube
Tim on Twitter
Tim on LinkedIn
Email tim@cleanpowerhour.com
Review Clean Power Hour on Apple Podcasts
The Clean Power Hour is produced by the Clean Power Consulting Group and created by Tim Montague. Contact us by email: CleanPowerHour@gmail.com
Corporate sponsors who share our mission to speed the energy transition are invited to check out https://www.cleanpowerhour.com/support/
The Clean Power Hour is brought to you by CPS America, maker of North America’s number one 3-phase string inverter, with over 6GW shipped in the US. With a focus on commercial and utility-scale solar and energy storage, the company partners with customers to provide unparalleled performance and service. The CPS America product lineup includes 3-phase string inverters from 25kW to 275kW, exceptional data communication and controls, and energy storage solutions designed for seamless integration with CPS America systems. Learn more at www.chintpowersystems.com
The Clean Power Hour is produced by the Clean Power Consulting Group and created by Tim Montague. Please subscribe on your favorite audio platform and on Youtube: bit.ly/cph-sub | www.CleanPowerHour.com | contact us by email: CleanPowerHour@gmail.com | Speeding the energy transition!
You know, humans are really good at a lot of things. So picking up two pigtails and plucking them together is very easy for a human to do in a second very hard for a robot to do. You know, we're focused on the heavy lifting, if you will. So, you know, the the two biggest sources of repetitive stress injury to workers are lifting torque tubes and lifting modules. And so we eliminate that. But all the fine motor things like flipping the modules and stuff like that are best done by humans today.
intro:Are you speeding the energy transition? Here at the Clean Power Hour, our hosts, Tim Montague and John Weaver bring you the best in solar batteries and clean technologies every week, I want to go deeper into decarbonisation. We do two, we're here to help you understand and command the commercial, residential and utility, solar, wind and storage industries. So let's get to it. Together, we can speed the energy transition.
Tim Montague:Welcome back to the Clean Power Hour, Matt, it's really good to see you again, we are going to be talking about what you're up to at Tara bass energy. It's been about a year maybe since we last spoke. And, you know, we know you as a software platform for utility scale solar, you're now going very hard after automation, which is very important because there aren't enough humans to do all the work that needs to get done in the clean energy transition. We need automation. The Clean Power Hour is brought to you by Denowatts. If you're a solar PV asset manager or performance engineer, you need better data and better business intelligence. With Denowatts, digital twin benchmarking technology, you get more accurate, efficient, and faster performance measurement results. The fourth generation Deno recently completed a technical review by DNV. You can download the report at Denowatts.com, that's D E N O W A T T S.com. Now back to the show. So let's just have a very high level, Matt, give us a status of terror base and just paint a broad picture for us. What is the company up to? And then let's geek out a little bit on your automation platform.
Matt Campbell:Sure, yeah. Good morning. Good to see you. Yeah, so we've, since we last spoke a lot of developments at Terra base. So and we view the solution to scaling utility scale solar as being a combination of digital and automation. I think it's it's easy to sort of compartmentalize between just a digital solution or just an automation solution. But we look at the effort holistically. So since we last spoke, you know, we've continued to scale a variety of our digital platforms. So we've got construction management system, that's like a digital solar construction system, we've got over five gigawatts of construction that's being managed in that platform. Now, here at RT plus, we're introducing a new software that helps you optimize the grading and Civil Works, which is a huge issue in the solar industry, how to eliminate grading, how to reduce the cost of foundations. So digital offers a lot of benefits there. And then on the automation front, since we spoke, we've released the 1.0 of our construction automation system, which is a combination of digital communications network, and an on site pop up factory. And those three, three things work together to help take the heavy lifting out of building a solar project.
Tim Montague:Yeah. So I'm a huge fan of creating a controlled environment, right for construction in general, right, it just makes humans more productive, it, you know, leads to higher quality work. And of course, it's great when conditions are really tough in the field, which they have been in the southwest this year. Right, very, very hot weather. And so this does reduce the risk factor for the humans involved in the project as well. Paint a more detailed picture, though, about this, this factory, this pop up factory that you're that you've designed and have now built and and, and give us some sense of the relative scale of this and, and how much production is coming out of it relative to standard construction methodologies. And, you know, let's talk about 100 megawatt plant. Of course, it depends on how many humans you throw at a project, how quickly it can get done, right? How many megawatts per week or month can get installed. So that's all relative, but at the end of the day, we're driving down the cost of LCL II. And so we have to create systems that are working for that goal, right. So give us a little more flavor on the on the system.
Matt Campbell:Yeah, so the how the system works is we send a pop up factory to the site. It consists of torque tube dispensers. A Module conveyance system, a robot for, for unloading packs and put it onto a conveyor. And then we have a workstation where the construction crew assembles sections of a tracker. So we call them tables, they're about 32 feet long. And basically, the robot takes these quite large panels. And the thing to note about solar panels is they've gotten about 40%, bigger and heavier in the last three years. So it's, it's really changed the, the strain of the of the activity of lifting panels. And when it's 123 in the Southwest US, that's a pretty tough job if you're doing that lift in that, you know, 85 pound panel every minute.
Tim Montague:Yeah, I was I was walking by a panel being unloaded yesterday here at already plus, and they're literally almost as big as a sheet of plywood. Now, they're, they're approaching four by eight.
Matt Campbell:That's right. Yeah, four by eight is the common dimension, except it's much heavier than a sheet of plywood. Yeah. And it's glass. So you gotta be careful, it doesn't break.
Tim Montague:And so are you automating the process, though, of actually picking up the panels and placing them on the torque tube.
Matt Campbell:That's right. So we use robotics to unload the pack. So So in the case of our pilot, we're building currently, we're using the new First Solar series seven panel, which is made in Ohio. And so we have a robotic system to unpack it. And it's quite a complicated challenge, because we're doing it outside. And so we have to do that quickly and without, you know, damaging panels. So that that robot loads that conveyor line, the conveyor line brings the panels down to the workstation where they're assembled. And then the final table is placed on to a delivery rover, which is an off road vehicle, that delivery rover is digitally controlled. So it knows, you know that we've got 200 different skews on the site, surprisingly, so different combinations of panels, orientations and torque tubes. And so our Digital Command Center will, will know what to build based on the build sequence, it will send the rover to the right location. Like it's kind of like a Tesla with your nice big digital map. And then it'll record the progress of the installation. And then it'll memorialize where it was installed with the serial numbers, where it's all kind of, and then all the analytics are available in our digital platform.
Tim Montague:I would imagine that torque tube with all the modules on it gets very heavy. So what kind of a arm you know, and what is the capabilities of that? It sounds like there's there's multiple types of robots involved in this. Yeah, pop up factory.
Matt Campbell:Yeah, so it's, the structure is about 1000 pounds. And, and of course, safety is the most important thing. And so as we designed our system, we took into account, you know, how do we keep that payload secure, and then it has to be installed with the kind of millimeter level precision. So we have this sort of computer controlled five access control system on our rover, that will align and, and secure the table onto the foundations, and of course, foundation. So you've got doing automation outside is very hard, because you've got, you do not have a controlled environment, you know, even in a factory, you know, like company like Tesla will have, you know, army of engineers trying to optimize an automation system, when the lighting is controlled, you're on a concrete slab, and it's 68.1 degrees, you know, we have, you know, minus 30 to plus 120, we've got mud, we've got bumps, we've got variability in the placement of the piles, they can, you know, so it's not a consistent landing pad, if you will. And so all that is based on the design of the system, and in terms of lifting the structure, we use, we grab it from below always, so we don't swing it from a crane or something. And that's to make sure that we've got a really secure grasp on the on the structure for for transport and landing.
Tim Montague:And how much human labor is involved in this process that you've just described for us taking panels off a conveyor belt, putting them onto the torque tube attaching them to the torque tube, yeah, wiring them up. Yeah. Is it even conceivable that robots will, can will do the wiring process.
Matt Campbell:You know, humans are really good at a lot of things. So picking up two pigtails and clicking them together is very easy for a human to do in a second very hard for a robot to do. You know, we're focused on the heavy lifting, if you will, so, you know, the the the two biggest sources of repetitive stress injury to workers are lifting torque tubes and lifting modules. And so we eliminate that But all the fine motor things like clipping the modules and stuff like that are best done by humans today. And so a lot of times people think automation, they're like, Oh, you're getting rid of jobs. But the reality is we're changing the jobs. We were creating new job categories, and we're making the work easier. But, but but certainly in the future, I think more automation will be possible. The Clean
Tim Montague:Power Hour is brought to you by CPS America. The maker of North America's number one three phase string inverter with over six gigawatts shipped in the US. The CPS America product lineup includes three phase string inverters ranging from 25 to 275 kW, their flagship inverter, the CPS 252 75, is designed to work with solar plants ranging from two megawatts to two gigawatts, the 250 to 75. pairs well, with CPS America's exceptional data communication controls and energy storage solutions, go to chin power systems.com. To find out more. Yeah, I like to say that we're all going to become a bot wranglers in some way shape or form, you know, with the advent of chat GPT. And now this explosion of, of similar tools. Truly, right, we all have to learn how to integrate AI into our lives in some way, shape, or form. And, and mechanical labor is no different. And I think that, you know, EPCs will will welcome this in time. It is an adjustment for some at first, sure. But truly the amount of solar that we need to install. And and the worsening working conditions. I mean, I just think it makes so much sense. So what have you learned so far? What's working? What have you had to iterate on? If you could just, you know, again, paint a little more flavor for us? Because, you know, it's, it's very easy to make a drawing of this. And you showed me a great digital dashboard that you have, which is super impressive. I can't wait to be able to show that to the world where you're tracking everything that's going on on the site. I mean, that is that's a game changer. I think if you're a construction company being able to see the progress in real time, basically, right? I mean, that's unheard of. And but But yeah, just paint us a little more nuanced about what what have you learned? And where have you met some significant challenges?
Matt Campbell:You know, most of the solar projects are very remote. And so you've got to be, it's like, it's like hiking the Appalachian Trail. You don't want to forget something in your pack. So you've got to be, you know, really thorough plan to make sure you've got all the tools and spares and everything. And I think we've done that. But I think certainly working under harsh conditions in a remote setting have presents its own set of challenges. I think the weather, very variable. I mean, we've had, you know, big dust tornadoes, we had a grazed by a hurricane or tropical storm. We've got you know, mud and dust and, you know, different lighting conditions that affect vision systems, and sensors. And you know, and you find all sorts of silly things like the, the reflective vest of the workers tripped a sensor, and we couldn't figure out why the sensor was acting up. It was reflecting off the vest. Yeah. So that's why that's why you do pilots, you find little things. I think the control of the packaging is important. So a lot of times the packaging disintegrates on a site, it's cracked, and you see cardboard boxes falling all over and stuff. So, you know. And then to do automation while on site, you need very good upstream supply chain. Is the material there on time, is it there's the quality meeting specifications? And so those are the kinds of things and we've been working with OEM partners to kind of integrate. So we know what materials come in, and we're ready for it. And but there's a lot to it. I think people fixate on the robot arm picking up a panel. And although that's the cool thing to look at, that's actually the smallest part of the equation.
Tim Montague:Yeah. So in terms of productivity, what are your estimate? The Delta is, you know, before and after an EPC were to integrate your system?
Matt Campbell:Yeah, I mean, we we estimate that with the existing generation, it's about a 25% difference for the same scope of activity. And we think in a next generation, it'd be about 50%. That's significant. Yeah, it's significant, but still a lot of work to do to get there. But it's, you know, last week, for example, we had a record week, we're ramping up our pilot currently. And like Friday, we set a record. We installed I think Almost 1300 panels with a robot? I'm not sure that's ever been done in a day before. That's a lot of glass. And with zero breakage? No, that's, you know, because a lot of times again, it's not really about just labor, it's about quality and getting rid of the stress on the workers and things like that.
Tim Montague:Yeah. So you have how many pilots running now? And what how is this activity scaling in the in the in the near future?
Matt Campbell:Yeah. So we've got one large commercial pilot underway. We've got more planned, you know, through the first half of next year, you know, our, we take a very pragmatic view, kind of walk, crawl, run, fly, and so we're, or no crawl, walk, run, fly. So we're somewhere between, we're walking, let's say, and we'll be still walking next year. You know, we had a mantra when I used to work at SunPower, you get good before you go fast. And so we're working on getting good. Because if you ramp too early, and come some clean tech companies ramped too early, then you start running into problems. And those problems can be expensive. So we're focused on process efficiency, quality. And once we're ready, then we'll scale towards the end of next year.
Tim Montague:You mentioned first solar. Can you talk about any other OEMs that you're working closely with on this platform?
Matt Campbell:Yeah, I mean, we, you know, been engaged with the major tracker companies. The, the tracker we're working with right now is with next tracker. And, of course, the market wants to see support for multiple trackers. And so that's, that's part of the roadmap. But But no, you know, all the OEMs are interested in, you know, driving the next wave of digital and automation. And so they're, they've been really great to work with, to kind of push this forward.
Tim Montague:Let's pivot a little bit and talk about already Plus, we're here in Las Vegas 2023 30,000, approximately energy professionals gathering. What are you looking forward to in the next three days? And if I'm a solar professional, what, you know, well, what kind of people are you looking to connect with here?
Matt Campbell:Yeah, I mean, you know, are you pluses, I guess the, the big annual event in the United States for solar. So it's always, really a lot of fun to come here, you know, when we come to our A plus part of it is to reconnect with our customer base. So you know, we've got customers from owners and EPCs, developers, engineering firms. And so we reconnect with our client base, we always like to meet new faces, you know, share the newest developments. But you know, primarily, it's packed with customer meetings. And I think as most people, these shows are extremely busy. So it's, yeah, we'll begin our steps in this week.
Tim Montague:Well, is there anything else that you'd like to talk about? I, you know, I'm a little handicapped. I don't know what I don't know. I'm excited that you're, you know, able to show off the automation platform the way you are. And, you know, even if you're not doing robotized construction, that platform for tracking what's going on on the site is going to be you know, very interesting, I think, to EPCs. And so we might see a, I guess, a hybrid emerge, right? Where some companies go all in on automation, but some go half in and but leverage your technology for tracking progress. And, you know, expediting This is what goes where, when, right, the more you can standardize, and factory eyes, that construction process, of course, it's going to just be more more efficient.
Matt Campbell:Yeah, exactly. I mean, we couldn't be more excited by that merging of the physical and the digital that that we're doing. And, and we have a lot of plans to expand that into really all aspects of the solar construction. You know, there's a lot of work that's been done for the past 10 years to use drones, drones to look for hotspots, drones to track construction progress. But we think that that's really just scratching the surface. If you really want to bring digitalization and transformation to solar construction. It's it's, it's how do i digitalize what's happening on the ground and what's happening in the supply chain and, you know, if you really want to change things, so that's, that's a lot of where our focus is. So that's sort of a halo around our construction automation system. In fact, that construction automation system had us build that out of necessity. But we see that it's a platform that can be extended, and and you know, the old The same as you, if you can't measure it, you can't improve it. But now that we can start measuring everything, the sky's the limit in terms of, you know, what's worker productivity by temperature, by geography by workforce, you know, how do we reduce idle time, you know, like. So, for example, might take a half an hour to get going in the morning, because people are finishing their coffee and stretching and how do we make that 20 minutes right, and now that we can measure it, we can help the PC drive operational improvements.
Tim Montague:The Clean Power Hour is brought to you by Denowatts. If you're a solar PV asset manager or performance engineer, you need better data and better business intelligence. With Denowatts, digital twin benchmarking technology, you get more accurate, efficient, and faster performance measurement results. The fourth generation Deno recently completed a technical review by DNV, you can download the report at Denowatts.com. That's D E N O W A T T S.com. Now back to the show. Well, thank you for visiting us here in booth 2269. It's great to see you again, and have a wonderful show. And please stay in touch we you know, of course, we'll follow your your press releases and announcements. But if if there's others at Tara base, who would like to come on the show, I love geeking out with other technologists in the company. And with that, I'll say, let's grow solar and storage. I'm Tim Montague. Hey, listeners. This is Tim, I want to give a shout out to all of you. I do this for you twice a week. Thank you for being here. Thank you for giving us your time. I really appreciate you and what you're all about. You are part and parcel of the energy transition, whether you're an energy professional today, or an aspiring energy professional. So thank you, I want to let you know that the Clean Power Hour has launched a listener survey. And it would mean so much to me. If you would go to clean power hour.com. Click on the About Us link right there on the main navigation that takes you to the about page. And you'll see a big graphic listener survey, just click on that graphic, and it takes just a couple of minutes. If you fill out the survey, I will send you a lovely baseball cap with our logo on it. The other thing I want our listeners to know is that this podcast is made possible by corporate sponsors. We have two wonderful sponsors today, chin power systems, the leading three phase string inverter manufacturer in North America, and Denowatts, a performance monitoring platform for utility scale solar. So check out CPS America and Denowatts. But we are very actively looking for additional support to make this show work. And you see here our media kit. With all the sponsor benefits and statistics about the show. You know we're dropping two episodes a week. We have now over 320,000 downloads on YouTube. And we're getting about 45,000 downloads per month. So this is a great way to bring your brand to our listeners and our listeners our decision makers in clean energy. This includes projects executives, engineers, finance, project management, and many other professionals who are making decisions about and developing designing, installing and making possible clean energy project. So check out clean power hour.com both our listener survey on the about us and our media kit and become a sponsor today. Thank you so much. Let's go solar and storage